Is a Rotary Feeder an airlock?
As mentioned in a previous post, naming conventions for airlocks are specific to the companies that manufacture them. Most names are a combination of industry terms, nomenclature and specific terminology relating to the manufacturer. It is important to note the term “airlock” is in relation to the functionality of this unique piece of equipment, which has two important functions:
-
- 1) Maintaining constant pressure within the system by keeping air from leaking between the airlock’s rotor and the housing. This separates the upper atmosphere from the lower atmosphere and ensures the material is moving downstream.
- 2) Metering the flow of material into the delivery system, which aligns with the throughput requirements of the material delivery system.
Most rotary airlocks today accomplish these two main functions, but rotary airlocks as a whole are uniquely different! This is certainly the case with the two main types of rotary airlocks that Precision Machine & Manufacturing (PMM) builds. One is a Rotary Feeder, which we also refer to as a Rotary Airlock Feeder and the other is a Rotary Valve, which we also refer to as a Rotary Valve Airlock. Functionally both are airlocks and metering devices. However, both serve different purposes, are used in different ways, and in a variety of material handling applications.
Airlocks come in all shapes and sizes! This is certainly true for the airlocks built by a small handful of manufacturers who are in the Pacific Northwest, and whose airlock design evolved from a century old wood products industry. This industry has been the conduit for a variety of important innovations and this certainly held true when it came to a northwest-inspired rotary airlock as well.
As wood is processed, there can be great variations in the size of material. These variations oftentimes cause blockages within a system, which oftentimes shut down an entire production line. As we all know, time is money, and frequent downtimes can be costly! In other parts of the country, most industrial manufacturing plants install some sort of size reduction device, such as a hammer mill, to reduce the size of the material prior to entering the airlock. Hammer mills are a great piece of equipment but are ineffective against organic materials such as wood, agriculture waste, biomass material, or plastics. These sorts of materials require special treatment so a solution emerged to develop an airlock with a razor-sharp piece of steel, which would cut the material prior to passing through the airlock. Essentially building a size reducer and an airlock into one! In theory, this was certainly a great idea, but functionally it took many years to perfect, and the R&D continues to this day.
Precision Machine & Manufacturing’s version of an airlock that is specifically designed and engineered to handle organic types of material is called a Rotary Airlock Feeder. PMM’s Rotary Airlock Feeder is equipped with a U.S. sourced hardened tool steel knife, which is razor sharp and combined with a helix rotor to create a shearing action in the upper part of the airlock. This combination effectively reduces the material size, which significantly reduces blockages downstream, while also operating as a highly effective airlock. Although our current rotary airlocks can be traced back to the original concept, today’s airlocks are equipped with a variety of important and specific variations, which are unique to the type of materials being conveyed and the overall temperature of the operational environment.
Over the last several decades, only a small number of manufacturers build a rotary airlock with a knife that is engineered specifically to move wood products, pulp & paper, biomass and alternative fuels. Each one of these manufacturers are located the Pacific Northwest and we are proud of our wood products heritage and how a single airlock has spawned an entirely new line of products, which today are used through the United States of America in a variety of material handling applications.
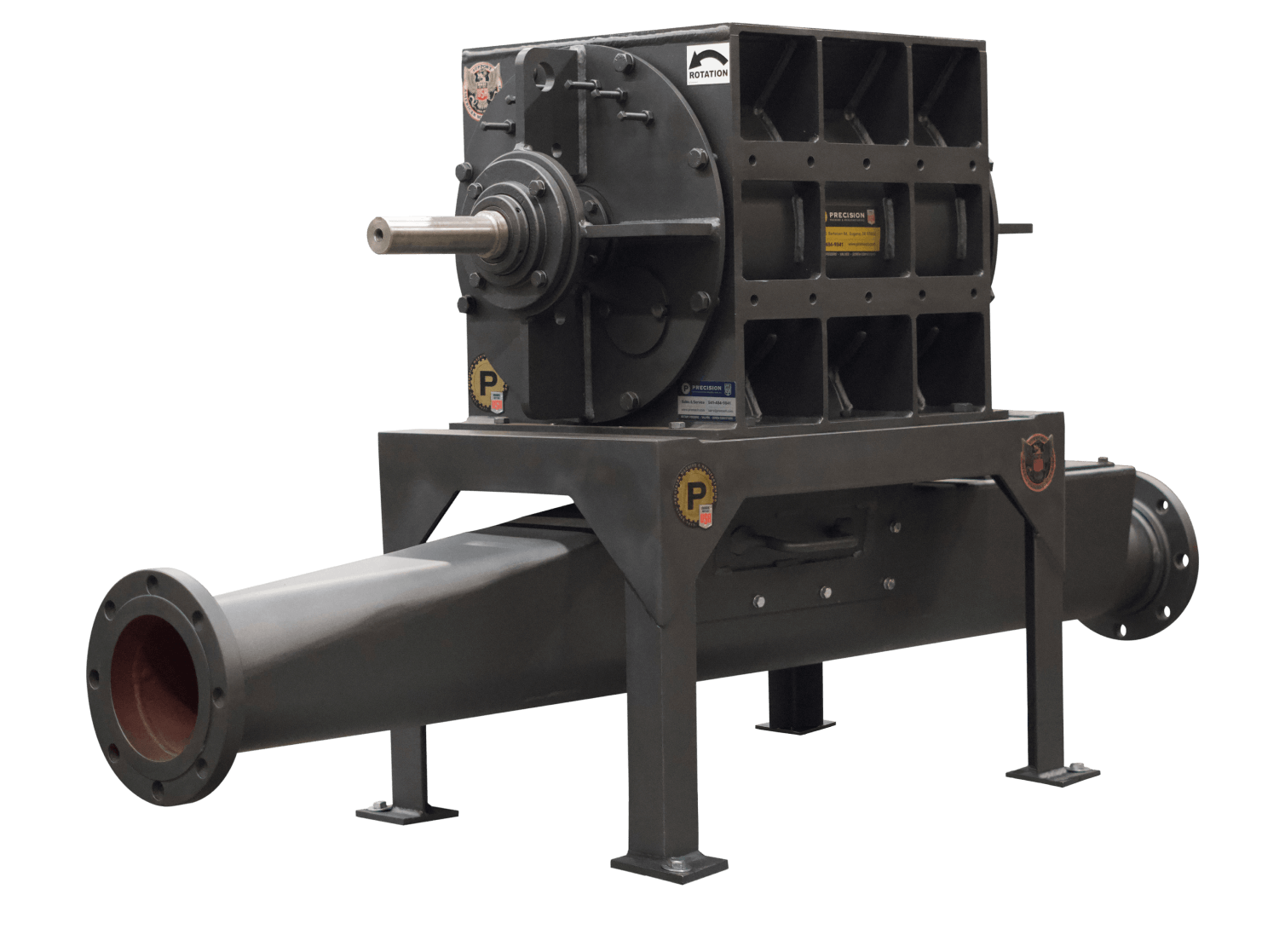